12 Ways in Which Toyota Create a Great Workplace
Last week I got the chance to visit Toyota, whose Toyota Production System has made it one of the most innovative companies on the planet. They are proud to have created a “happy workplace, where employees can work with confidence, vigor and enthusiasm,” and were recognised for the second year running in February 2016 by the Sunday Times Best Workplace list.
Here’s my reflections on the look-and-feel of a great workplace.
Hi, we are Happy
We are leading a movement to create happy, empowered and productive workplaces.
How can we help you and your people to find joy in at least 80% of your work?
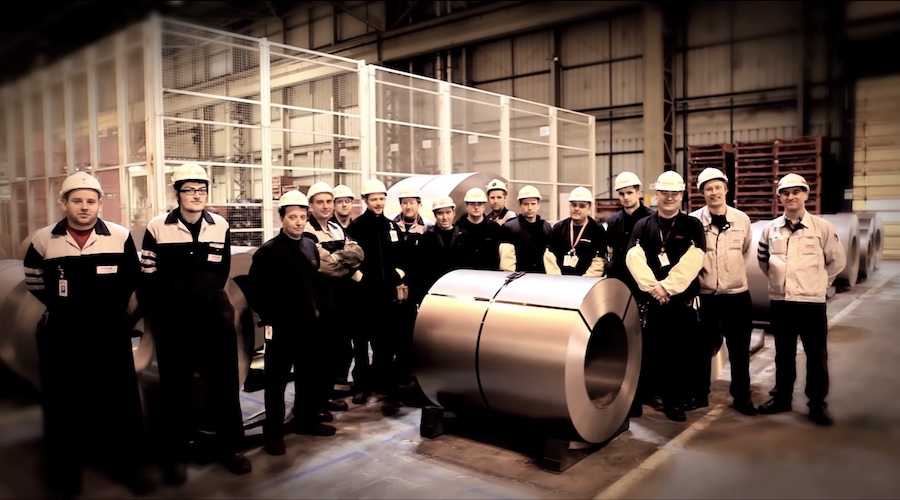
1. More people, less machines
The first surprise was that the assembly line was not full of robots. Most of the machinery looked as if it could have been in place 30 years ago. We were told that they have actually reduced the level of automation in recent years. “People are more flexible than machines,” was one response.
There was also no SAP or ERP system in evidence. Instead, the key monitoring tool was developed in Excel. “We want a system that adapts to the way we work, not to have to adapt to the way an existing piece of software works.” And this was no paperless office. Charts and written sheets were everywhere.
2. Two improvements from each member every month
“Never be satisfied with what you have got” is a core principle at Toyota. Every “member” (as staff are called) is expected to come up with two “kaizens” (or ideas for improvement) each month. Indeed they are trained in fabrication and welding to enable them to be able to test out their ideas.
Time is dedicated to kaizen: Each member is allocated 15 minutes a day to identify possible improvements. Managers will try and avoid opposing a change, even if it has been tried before and not worked. A key point of kaizen is personal development: “The learning comes from the journey.”
3. Intrinsic motivation, not money
There are no rewards for any financial gain resulting from the improvements people make. “We don’t want our people driven by money but by the desire to improve the process.” There are also no individual bonuses, only collective bonuses.
4. Standardise, then improve
There is a sense of empowerment and engagement wherever you go at Toyota. But there is no sense of anarchy. Every process is carefully documented. “Every member is encouraged to improve the current process, but that standardisation makes it easy to return to the old process if the idea doesn’t work.” If the idea works, then the new approach is standardised and written down as a process by the member who created the improvement.
“Without standardisation there can be no kaizen,” said Toyota founder Taiichi Ohno.
4. Each Toyota assembly line is different
When a new engine is created, or a new car rolled out, each plant will be equipped with the same assembly line and set of standardised processes. However each plant is continually innovating and, although yokoten (sharing) means many innovations get adopted at other plants, some don’t. The expectation that every member is continually seeking improvement means that every Toyota assembly line is different. There is standardisation of processes on each line but seems to be no desire for standardisation across sites.
The Toyota plant I visited in Deeside had a slightly old fashioned look to it. But this is apparently the most productive Toyota assembly line on the planet, being the first to achieve an engine every 48 seconds.
5. Small changes matter
A kaizen doesn’t have to be huge. One example was a lever that popped up a screw, meaning the member didn’t need to bend down to pick it up. It was estimated to save two tenths of a second.
“We build ten million cars a year. Save two tenths of a second on each one and that’s a gain of 560 person hours.” Do one thousand of those a month (two for each of the 500 staff at the Deeside plant) and, if they are shared across the whole company, you’ve gained half a million person hours.
6. Quality Control Circles: Full involvement
Twice a month the assembly lines shut down for half an hour as every member gathers into their QCCs (Quality Control Circles). Here they study the data and learn more about what is going on in their section and throughout the company.
This may result in further improvements but “that is not the point. The aim is development,” and that is what the carefully laid out QCC plans focus on.
7. A no blame culture
“We would never blame the individual. If something goes wrong, it is the process that has gone wrong.”
One of the two key pillars of the Toyota system is jidoka. Every member can pull a cord to stop the belt if there is a problem to help eliminate the root cause. Team leaders must never criticise a member for pulling the cord, as “we want them to pull the cord.”
“If you blame somebody for failure, all that will happen is people will start sweeping problems under the carpet.”
8. Systems to prevent error
I knew that Deming (the US management theorist that had such influence on Japanese methods) was clear that errors are caused by processes not by people. But visiting a Toyota assembly line really showed what he meant. Members will repeat the same process 150 times in a two hour session. It would be easy to miss a step or use the wrong part if the process allowed it.
Many of the kaizen improvements specifically prevent that. Buckets have green lights which go off if a hand has reached in to collect a part, so you know if you’ve forgotten it. With one component it was too easy to pick up two, so the delivery was altered to physically prevent that.
The member we watched was working alternately on different engines with different spark plugs. If both types of spark plugs were available and the member picked the wrong set, that would not be “human error” but process error. So a plastic shield swings across between the two sets so only the correct one is uncovered. As backup (in case the shield fails) a green light goes on over the correct set of plugs. It is impossible to accidentally use the wrong plugs.
It is all fairly low tech but these are simple systems that prevent human error by making it as difficult as possible to make that error. This is known as “poka-yoke” or “mistake proofing” and is intrinsic to the Toyota approach. If your system allows somebody to make a mistake, it is the system that is wrong, not the person.
9. It’s all about the people
“Our greatest resource Is flexible, motivated members.” Respect for people sits alongside continuous improvement at the core of The Toyota Way. “When you hire two hands you get a brain free. Clever people we have here.”
Managers are there to support. The development of the members is the most important thing you can do. “We build people before we build cars.”
In the standard management diagram, the front-line staff are at the bottom and the top managers are at the top. At Toyota, it is the other way round, clearly labelled that the role of managers is to support their members. They are expected to coach them and to ask “what can I do to help?”
10. Recruit for attitude, train for skills
“We can train people in the skills they need.” They recruit for good communication, teamwork, willingness to improve. “It is not that they have the best skills but the right team fit.”
11. Get them to do the job in the recruitment process
Those who know me will know this is my core requirement for effective recruitment. But Toyota take it to an extra level. Before they are invited to interview, applicants must spend a full day on an assembly line. Not the real one, but a mock assembly line. They are even asked to come up with one or two kaizen improvements at the end of it.
“We used to have people quitting on their first day, when they realised what they had to do. We don’t get that any more. If they are not up to it, they quit on that mock day.”
12. It’s about people, not money
One visitor asked if they have costed the time “lost” in working on kaizen and quality circles and compared it to the benefits that result and can show it makes financial sense.
The Toyota representative looks slightly baffled. It is one of those moments when you see two people working from completely different assumptions. It seems a calculation that Toyota would never see the need to carry out.
“We will never focus purely on cost,” he explains. “Development of the members is the most important thing you can do, our biggest resource.”
I left feeling that Toyota is truly a remarkable workplace. Those twin pillars of respect for people and continuous improvement seem genuine and embedded in everything they do.
The Toyota system came to widespread attention in the West when Womack and Jones of MIT wrote about it, defining it as “Lean Thinking.” However, their backgrounds meant they focused on the processes, such as cutting out waste, and largely ignored the people element.
It has even been said that founder Taiichi Ohno was very happy that the Toyota ideas had been so misunderstood in the West, by focusing on elements like the seven wastes, that were not actually the core element. (See “Did Toyota fool the Lean community?”)
Deeside is the only Toyota plant in Europe that helps other organisations implement ideas like Lean and continuous improvement. But many organisations, they feel, are not able to be helped in this way. The NHS is one example: “Just too many restrictive practices.”
The visit was part of the excellent Onsite Insights visits programme. Do contact them to find how you can get first hand experience of great companies (including Happy!).
Keep informed about happy workplaces
Sign up to Henry's monthly Happy Manifesto newsletter, full of tips and inspiration to help you to create a happy, engaged workplace.
Learn the 10 core principles to create a happy and productive workplace in Henry Stewart's book, The Happy Manifesto.
Henry's Most Popular Blogs
- 8 Companies That Celebrate Mistakes
- 9 Benefits of Having Happy Employees
- 321Zero: How I Solved my Email Overload
- 16 Companies That Don't Have Managers
- 5 Big Companies Who Swear by Mindfulness
- 49 Steps to a Happy Workplace
- A Four Day Week? Let's Start With a Four Day August
- Google: Hire Great People and Give Them Lots of Autonomy
- Buurtzorg: No Managers, Just Great Care From a Nurse-Led Service
- 30 Steps to Joy at Work: Get More Done by Being Less Busy
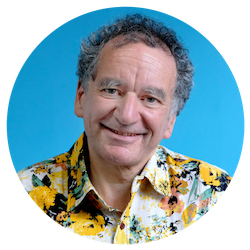
Henry Stewart, Founder and Chief Happiness Officer
Henry is founder and Chief Happiness Officer of Happy Ltd, originally set up as Happy Computers in 1987. Inspired by Ricardo Semler’s book Maverick, he has built a company which has won multiple awards for some of the best customer service in the country and being one of the UK’s best places to work.
Henry was listed in the Guru Radar of the Thinkers 50 list of the most influential management thinkers in the world. "He is one of the thinkers who we believe will shape the future of business," explained list compiler Stuart Crainer.
His first book, Relax, was published in 2009. His second book, the Happy Manifesto, was published in 2013 and was short-listed for Business Book of the Year.
You can find Henry on LinkedIn and follow @happyhenry on Twitter.
Next Conference: Women in Leadership Online Conference
Save the date for our online conference on 12th November 2025, celebrating women in leadership.
You will hear from inspiring female leaders about how they have created happy and empowered workplaces.
There will be interaction, discussion, space for reflection and opportunities to network with other leaders.
Related courses
The Happy Leadership Programme
Brave Leadership: One-Year Leadership Development Programme for Women
Level 7 Senior Leadership Apprenticeship Programme
Not what you need? Take a look at all of our off-the-shelf Leadership and Management programmes.